After 55 years in maritime construction, the latter 35 of which were focused on marina development, Tony Mair of Orakei Marina Development Ltd (formerly Mair & Associates) has retired. A lifetime member of the Institute of Professional Engineers of New Zealand and a lifelong boater, Mair leaves his signature on a wide range of marinas in his native New Zealand, elsewhere in Asia Pacific, and beyond. He has been directly involved in the marketing and sale of over 6,000 berths and no fewer than 16 marina projects. Marina World talks to him about his extraordinary contribution to the marina industry.
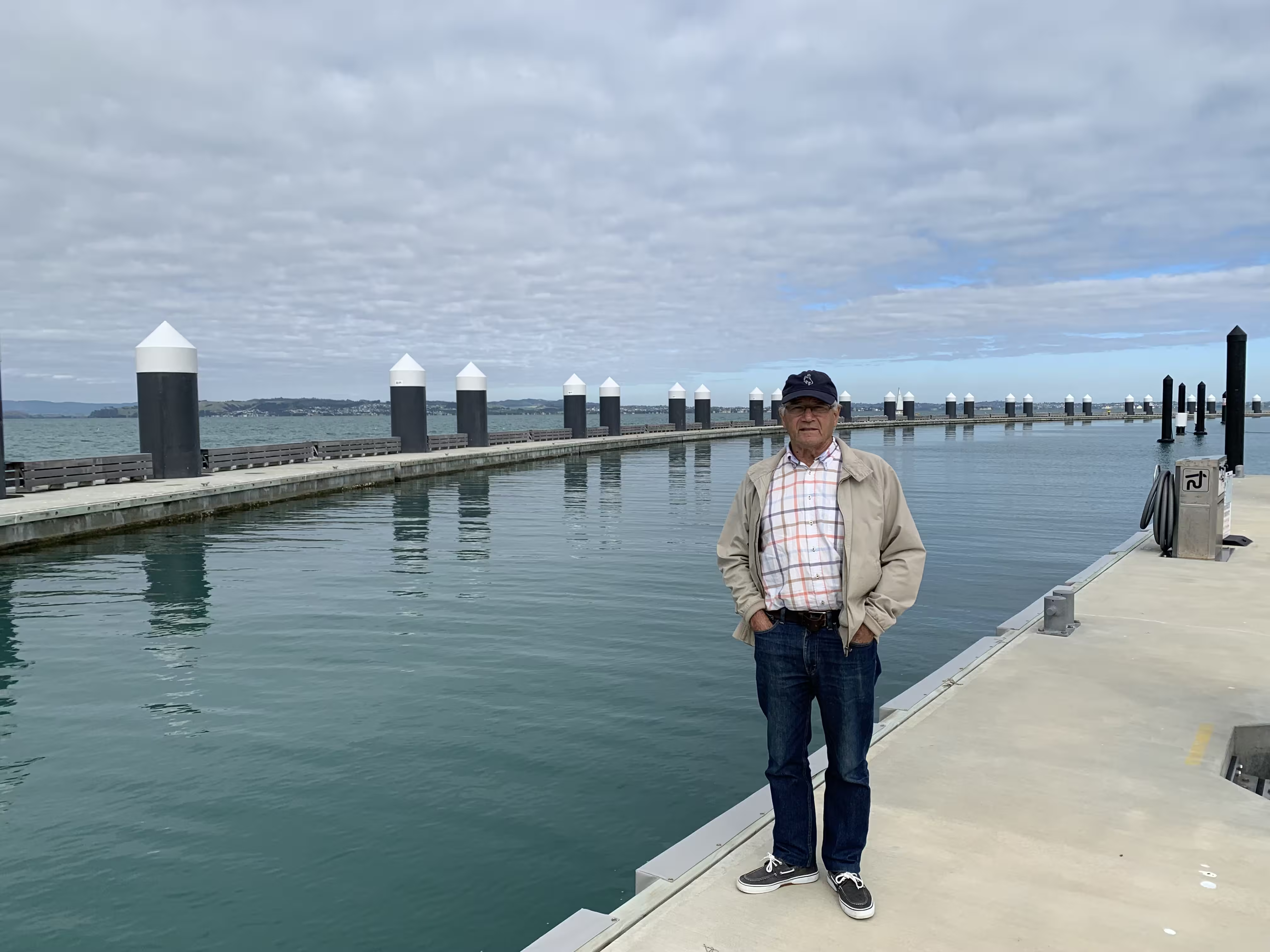
Q: How did your involvement in marina construction begin?
A: After graduating as a civil engineer in 1968 under a cadetship with Wilkins and Davies Construction, a company partially owned by Taylor Woodrow in England, I worked on numerous marine engineering projects in New Zealand, Samoa, Fiji, Malaysia and Borneo. In 1980, Wilkins and Davies (W&D) started a marina division and, as a keen boatie, I was asked to lead the operation.
Q: Where was your first marina project and what were the challenges in developing it?
A: The first project was Westpark, a 604-berth marina located in the upper reaches of Auckland Harbour. At the time – back in 1979/80 – there were only two marinas in New Zealand. Both of these had floating structures that utilised timber plank decking with steel tubes and glass fibre tubs for floatation. This didn’t suit my vision. I searched the world for a proprietary product and travelled to Bellingham Marine (BMI) in the USA and secured the South Pacific manufacturing rights for the patented Unifloat floating concrete dock system.
W&D and BMI developed a great relationship with the original owner of Bellingham Marine, the late Peter Gaasland, and his chief executive Larry Halgren (now heading up Halgren & Associates). Over the years, I have always been a fan of concrete floating structures over other materials.
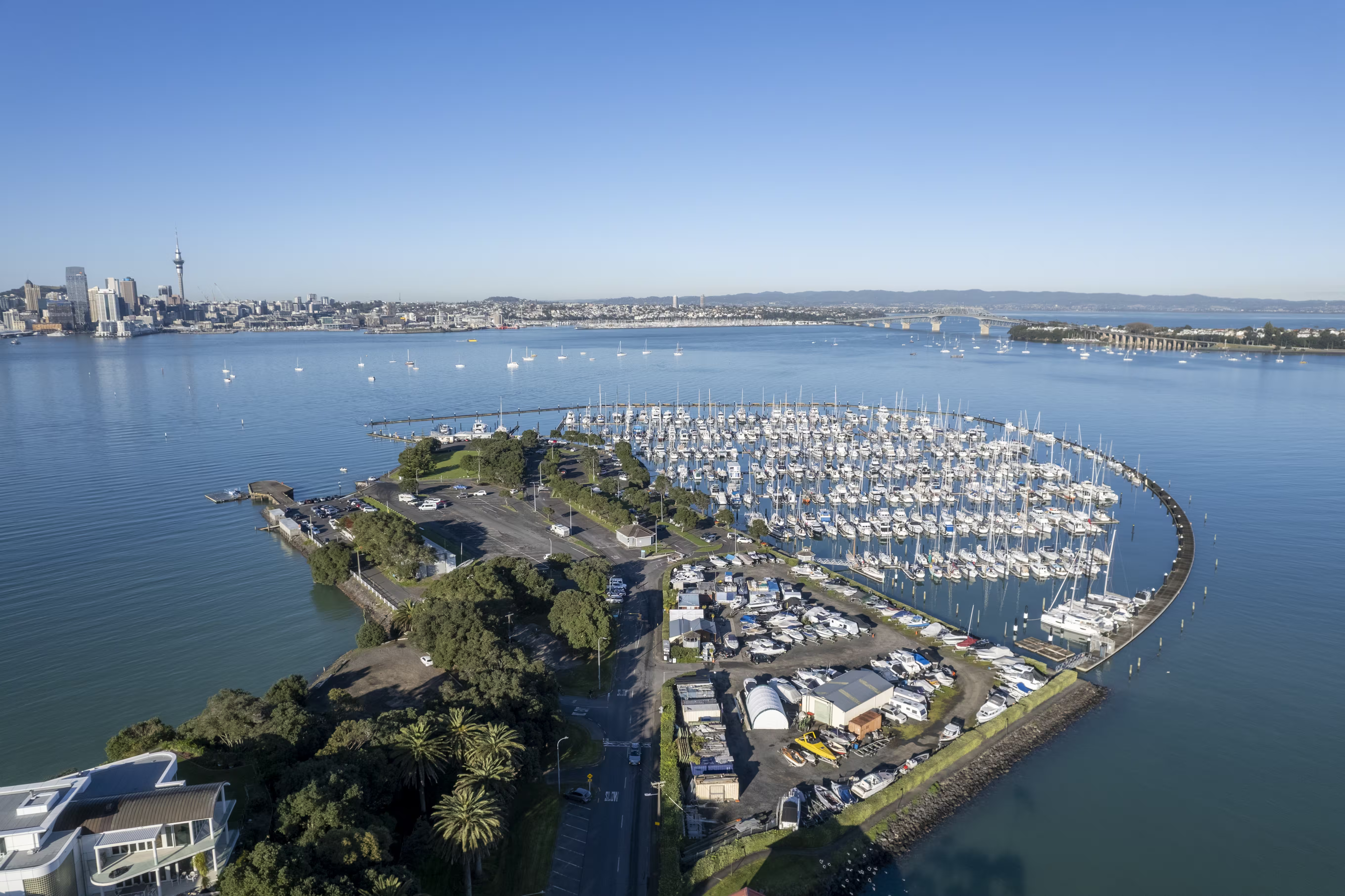
Q: Do you think completion of Westpark Marina focused the industry on marina opportunities?
The W&D marina division grew quickly with 60 staff! We carried out all aspects of development, from the initial site feasibility studies through design, marketing and sale of the berths, and construction. Yes, the projects came, including: Mana Marina (100 berths); Gulf Harbour (966 berths); Pine Harbour (550 berths); Buckland Beach Marina (100 berths); Bayswater Marina (440 berths); and Townsville Marina (200 berths).
During this time, we carried out many feasibility studies to determine whether or not a specific site had sufficient attributes to warrant the complicated and expensive planning and consent process, which at the time typically took between three and eight years in New Zealand. As a point of interest, this can now take many more years due to the increased hurdles a maritime project has to pass and the complexities with the environmental issues and cultural inclusion.
Q: Why did you leave Wilkins & Davies?
A: Unfortunately, W&D closed down following the brutal 1989 financial meltdown and this is when I continued on with marina development in my own right. Between 1989 and 1994, I owned and operated the construction company Marine Piling & Construction Ltd, with a partner, and completed a range of projects which required specialist plant and expertise, such as wharf construction in Auckland, Devonport Naval Base, Onehunga and the Chatham Islands. We also designed and built the Maritime Museum marina in Auckland and demolished the old floating structures at Half Moon Bay Marina and replaced it with Unifloat.
After 1994, Mair & Associates dedicated the team to the development of Orakei Marina in downtown Auckland, Opua Marina in the Bay of Islands and Tutukaka Marina. We were involved with Whangamata Marina and, in 2006, prepared the initial feasibility report for the proposed Sandspit Marina project. We consulted to Napier Yacht Club to boost berth sales and carried out a feasibility study for the proposed marina in Queenstown.
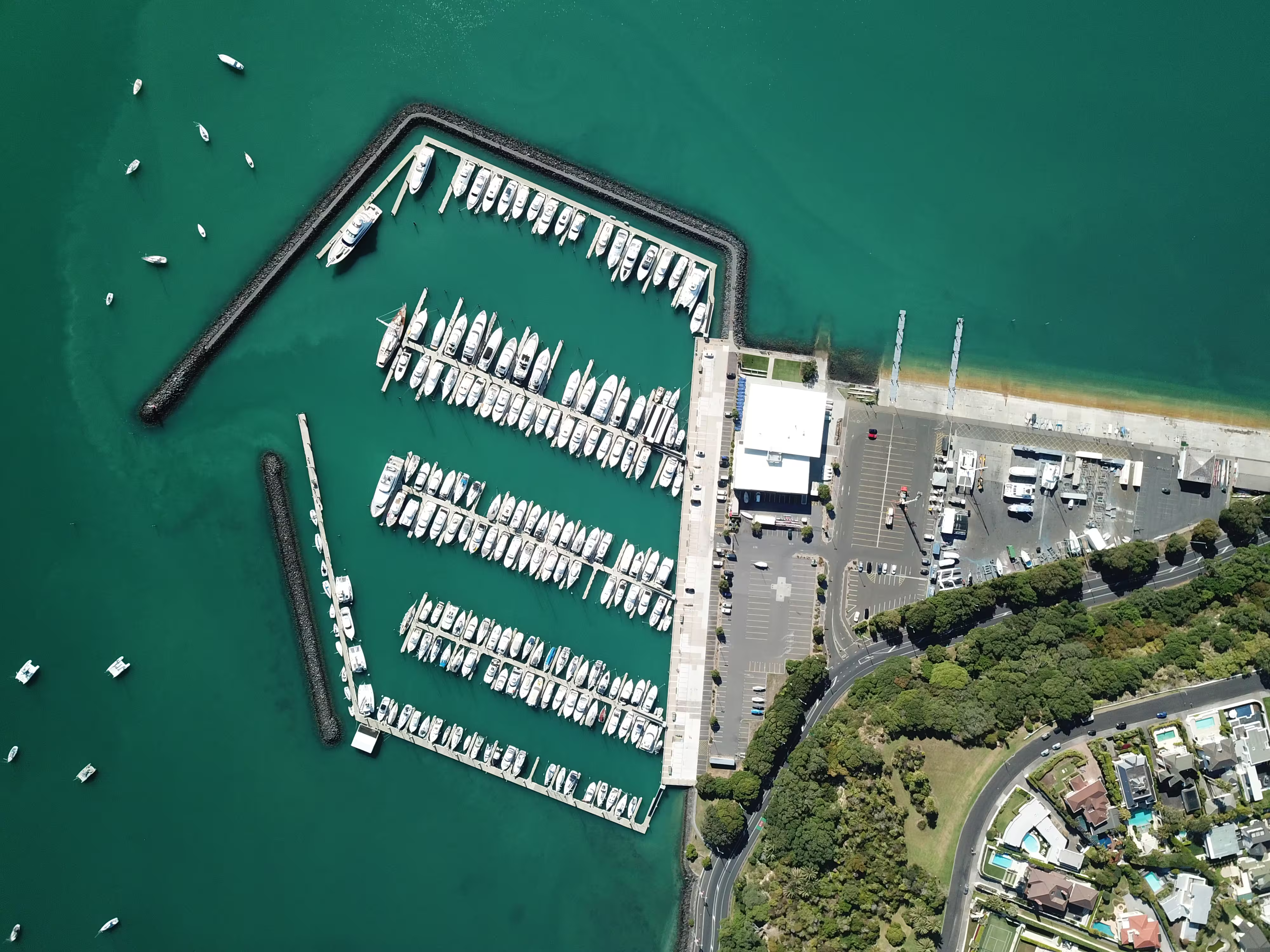
Q: Why do you think Orakei Marina Development is so successful?
A: We’ve earned the reputation of being New Zealand’s leading marina developer and I think we’ve been successful because we’ve kept control of all aspects of development within the group, which includes associations with at least 15 specialist consultants whose combined expertise has enabled us to successfully complete many difficult projects. Our projects have also been completed on time and on budget, using the right equipment. And we never go out for tender but negotiate the construction contracts with highly experienced companies.
We have the in-house resources to fund our projects and have the backing of the Bank of New Zealand. Legal documentation, including the registered prospectus to enable berths to be sold, is an extremely complicated and important component of the process and our legal team is highly experienced with this. Our marketing and sales people have the knowledge to sell the berth licences in sufficient numbers to eliminate financial risks.
Q: What do you think have been the biggest changes in marina development over the past 35 years?
A: Probably, the biggest change is the increase in berth size. Back in 1980, berth lengths ranged from 8 to 18m, with the majority at 10 to 12m. Today, berth lengths start at 12m and range up to 40m (excluding megayacht berthing) with an average length of 18m. Berth widths have also increased over this period.
In the eighties, power was supplied by small transformers with one 10 amp outlet for every two vessels whereas, today, the power modules start at 2 x 16 amp outlets up to 64 amp 3 phase plus a couple of 32 amp for each vessel.
Piling has changed. In New Zealand, the marina piles were initially tanalised treated pine and at Westpark Marina for example – which is now over 40 years old – the timber piles are still doing a fine job. Today, however, because the treatment doesn’t contain arsenic, the timber piles don’t last and require a plastic sleeve for protection against attack.
Galvanised metalwork has now been replaced with stainless steel, and concrete quality has improved. Construction equipment changed dramatically during my career. As a cadet engineer with Wilkins & Davies in 1963 we drove piles in New Zealand’s first marina in Auckland using a steam hammer. This progressed to drop hammers, diesel hammers and later “vibro” hammers.
Dredging was initially by clamshell and dragline with cutter suction being used at Westpark in 1982. Today’s very efficient and computer controlled hydraulic back hoes offer a huge advantage.
Mudcreting technology has made it possible to reclaim land utilising the soft marine silts as disposal at sea is now very problematic. Costs have also risen of course. When we started selling in 1980, the cost of a “licence to occupy” ranged from $12,000 to $50,000. Today, prices are $300,000 to $1,000,000.
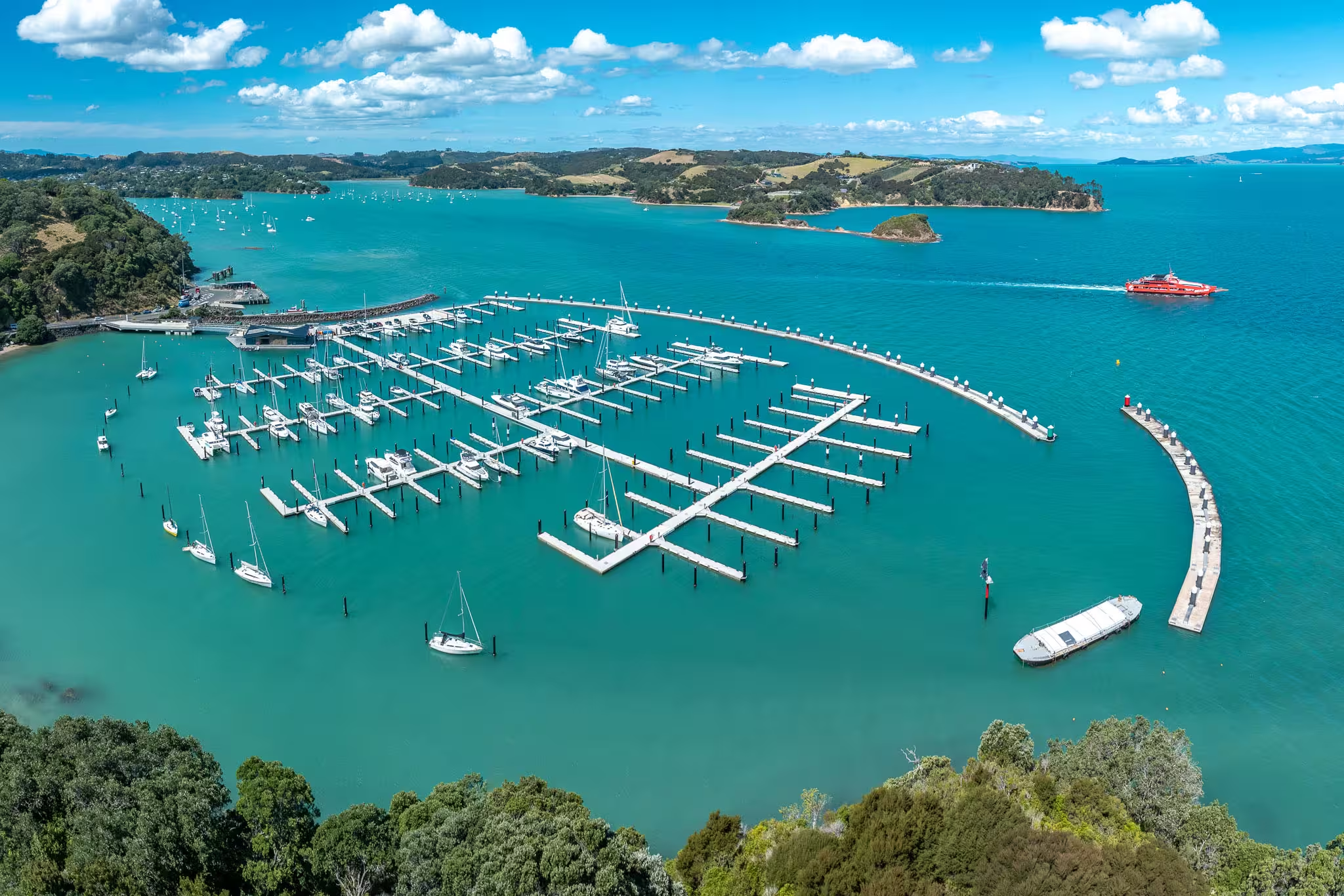
Building the last Mair marina
Tony Mair personally financed and coordinated a number of projects to completion throughout his career, including the green field marinas at Tutukaka, Opua, Orakei and, most recently, Waiheke Island Marina at Kennedy Point. Waiheke called for significant innovation as it sits in ecologically sensitive waters, and made for a challenging finale to Mair’s career.
First, developers had to determine how best to shelter 180 marina berths from wave fetch and ferry wakes without disturbing a colony of ‘Little Penguins’. A traditional rock-pile breakwater would have impacted currents and the area’s delicate flora and fauna, together with deep water and a very soft seabed. Second, the marina project had no land, and all facilities needed to be floating, including the office and car park.
The solution included construction of possibly the world’s largest floating marina breakwater; an elegant arc that mirrors the scalloped coastline of the island. It was built by Heron Construction, which manufactured the huge breakwater sections under licence to SF Marina in Sweden and towed them 145km to the site. Mair says that his association with Lars Odhe and the team at SF Marina was rewarding and memorable.
The 460m of curved attenuators comprised 23 x SFBW600 series floating concrete pontoons, each measuring 20m x 6m x 4m and weighing 220 tonnes; six on the western section and 17 on the main portion. The pontoons have a draught of 3.4m with 600mm freeboard plus a wave splash structure. Each pontoon is held by two piles 35m long x 1.5m in diameter. The pontoons are connected via SF Marina’s patented coupling system that absorbs and distributes stress loads.
The floating office and 76-vehicle car park are built on top of 27 x SF1250 concrete pontoons stressed together. Like the attenuators, they are engineered to be exceptionally stable and unsinkable. Rainwater is channelled from the platforms and filtered before being returned to the ocean. Building on top of an SF Marina floating concrete platform is not new. In Sweden, a two-storey, 33-room hotel uses similar SF pontoons for its floatation.
This article was originally published in issue 149 of Marina World magazine. Click here to read the online version.